This project aims at developing a flexible manipulator for picking. Fruit or vegetable picking requires a compliant and dexterous grip to guarantee the integrity of the object as well as a flexible carrying structure to be able to navigate between the branches without damaging them. The objective is to develop a continuous and jointless proboscis robot operated by remote motors and cables, similar to the tendons in a human hand. The project is divided into 3 main issues well known in the field of robotics, namely design, modeling and control. These 3 aspects are actually very intertwined for this kind of complex systems. A good design with a good integration of actuators and sensors facilitates enormously the control by means of an adequate modeling which answers at the same time to a certain realism and an efficiency of calculation.
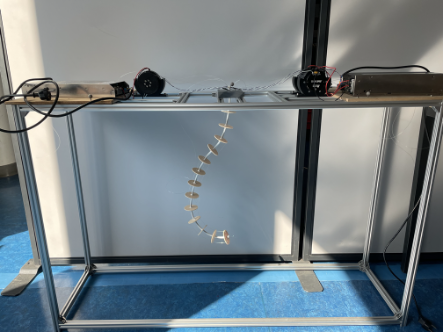
The context
In the context of the fight against global warming and unprecedented technological convergence (digital, artificial intelligence, etc.), agriculture must reinvent itself in order to produce better, while respecting the environment and human health. Agricultural robotics is one of the levers of this transformation. It is a promising solution for meeting the environmental and health challenges currently facing France and all other developed countries. The urgency of climate change will require an ever greater reduction in the use of inputs (pesticides, water, etc.) and fossil fuels. In addition, the agricultural sector suffers from a lack of attractiveness and a negative image among many young people (rurality, repetitive tasks, exhaustion, economic difficulties, isolation, etc.). Digitization and robotization will allow the valorization of this profession and will relieve the farmer of repetitive and tiring tasks such as weeding, carrying, picking and regular maintenance of crops.
The objectives
The primary scientific objective is to address the three main challenges of design, modeling, and control, in a simultaneous and integrated approach, sometimes referred to as co-design (hardware and software).
The targeted robotic system exhibits characteristics akin to a trunk, approximately one meter in length, with the capability to assume multiple stable configurations. Within the laboratory, two prototypes of continuous flexible manipulators have been developed to explore diverse solutions. The initial prototype features a backbone composed of braided metallic wires and low-friction material disks facilitating cable passage. The actuation involves nylon cables and servo motors with force control to ensure cable tension within predefined limits. Conversely, the second prototype, crafted from printed TPU, incorporates an antagonistic cables structure where a single motor actuates two antagonistic cables. This design inherently maintains minimal tension in the cables throughout its operation.
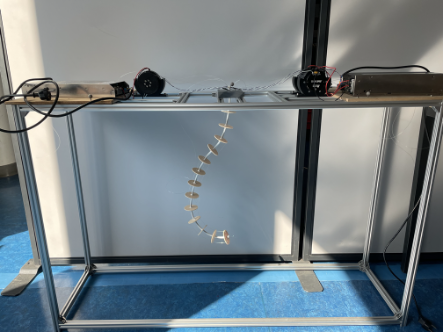
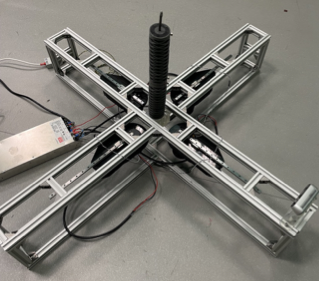
Two main approaches are studied regarding the control of these manipulators. The manipulator with braided metallic wires currently implements an open-loop control based on data. Its workspace has been explored to learn the inverse geometric model (cable length to pull as a function of the 3D position of the end effector) using a neural network. Conversely, the TPU manipulator implements perception-based control. The concept is to reconstruct its shape in space using stereo cameras to control the end effector.
The results
Recent findings have highlighted the viability of employing data-driven control in the context of cable-driven flexible manipulators. Whether for static tasks (reaching tasks) or dynamic tasks (trajectory tracking), the achieved precision is sufficient. Furthermore, the study of the system’s robustness and repeatability has showcased its ability to perform various tasks in its working environment repetitively with millimetric variability.
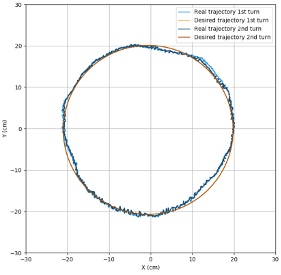
Partnerships and collaborations
The members of the Roboterrium – Equipex Tirrex network are partners in the project.